The BM-230 molecular distillation equipment is a cutting-edge molecular distillation apparatus designed for high-purity separation of heat-sensitive materials. Its advanced stainless-steel structure minimizes internal pressure and overheating risks, ensuring superior energy efficiency. Equipped with a triple-layer cold trap and thin-film scraping technology, it maximizes gas-to-surface contact for optimal condensation performance.
Featuring a 0.5 m² evaporation area and 8–30 kg/h feed capacity, the BM-230 molecular distillation equipment operates at -90–220℃ with a 200W motor. Ideal for pharmaceuticals, essential oils, and specialty chemicals, it integrates degassing, heating, and vacuum control systems for seamless industrial-scale processing.
Key Features of the BM-230 Molecular Distillation Equipment:
Advanced Stainless Steel Construction: Minimizes overheating risks and internal pressure while ensuring energy efficiency and durability.
Triple-Layer Cold Trap Design: Features windowed traps and forced gas flow paths for enhanced condensation efficiency and energy savings.
High-Capacity Processing: Offers a 0.5 m² evaporation area with a feed rate of 8–30 kg/h, suitable for industrial-scale applications.
Wide Temperature Range: Operates between -90–220°C, ideal for heat-sensitive materials like pharmaceuticals and essential oils.
Integrated Control Systems: Includes degassing, heating, vacuum, and cooling systems for precise, automated operation.
Thin-Film Scraping Technology: Ensures uniform liquid distribution and maximizes heat transfer efficiency during distillation.
Applications of the BM-230 Molecular Distillation Equipment:
Pharmaceutical Purification: Ideal for separating heat-sensitive active pharmaceutical ingredients (APIs) and synthesizing high-purity compounds like omega-3 fatty acids without thermal degradation.
Essential Oil Refinement: Enhances aroma and purity in critical industries such as cosmetics and aromatherapy by preserving volatile terpenes and delicate organic components.
Specialty Chemical Production: Processes temperature-sensitive materials (e.g., polymer additives, liquid crystals) requiring precise molecular separation and low-pressure operation.
Food Additive Manufacturing: Extracts natural flavors, vitamins, and nutraceuticals while maintaining nutritional integrity and compliance with food safety standards.
Advanced Material Research: Enables nanomaterial development and advanced lubricant refining in academic and industrial laboratories.
Competitive Advantages of Our Equipment vs. Competitors:
Global Recognition & Proven Reliability: Widely adopted by universities, research labs, and industrial facilities across 20+ countries, demonstrating trusted performance in diverse settings.
Unmatched Cost-Effectiveness: Combines premium functionality with competitive pricing, eliminating compromises between budget and quality.
Comprehensive Technical Support: Expert troubleshooting and real-time guidance ensure seamless integration and minimal downtime.
End-to-End Service Network: International distribution channels and rapid spare-part availability guarantee prompt post-purchase assistance globally.
Innovation-Driven R&D: A young, agile engineering team continuously optimizes designs for enhanced efficiency and user-centric operation.
Working principle of BM-230 molecular distillation apparatus:
The BM-230 molecular distillation apparatus operates by heating a thin-film feed material under high vacuum. Volatile components evaporate from the heated surface and immediately condense on a nearby cooled condenser (<5 cm path). This minimized travel distance prevents re-evaporation, enabling efficient separation of heat-sensitive compounds at lower temperatures. Non-volatile residues exit as bottom product, while distillate collects separately. Ideal for high-boiling-point or thermally unstable substances.
Maintenance Guidelines for BM-230 Molecular Distillation Equipment:
Seal Lubrication & Inspection: Regularly clean and lubricate seals (every 5-8 uses or 72 hours) with vacuum grease to prevent leakage and ensure airtight performance.
Electrical Safety: Keep electrical components dry; avoid water exposure. Conduct maintenance only after disconnecting power to prevent hazards.
Glass Component Care: Handle glass parts gently to avoid cracks. Clean residues with soft cloths and neutral detergents, then dry thoroughly to prevent thermal stress.
Interface Management: Apply minimal vacuum grease to glass interfaces during reassembly, rotating components for even distribution.
PTFE Switch Handling: Avoid over-tightening PTFE valves/switches during operation to prevent deformation or irreversible damage.
Preventive Checks: Inspect shafts and sealing rings monthly for debris, wiping surfaces with lint-free cloths and reapplying lubricants as needed.
Application Case & Customer Feedback
The BM-230 molecular distillation apparatus is widely used in pharmaceutical purification. A European nutraceutical company employed it to isolate high-purity omega-3 fatty acids from fish oil. Under optimized vacuum (0.001 mbar) and a gentle heating profile (120°C), the system achieved 99.5% purity while preserving thermally sensitive EPA/DHA structures, avoiding degradation seen in traditional distillation. Post-processing, residual contaminants were reduced by 98%, meeting stringent EU regulatory standards.
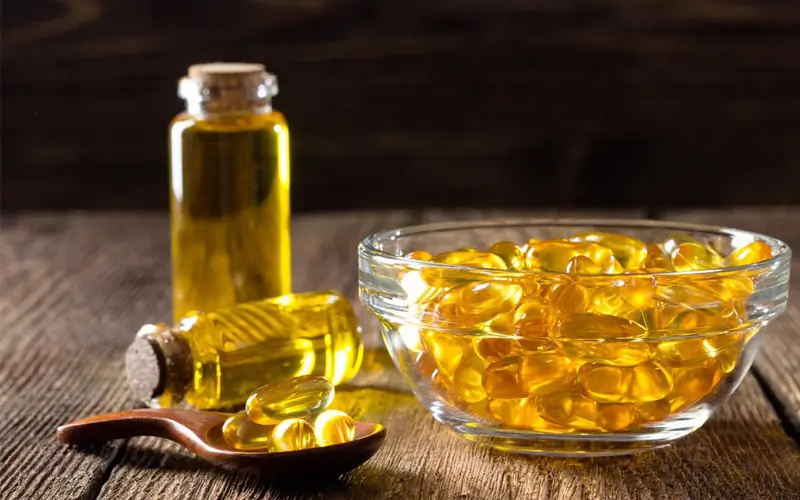
Customer Review:
"After switching to BM-230 molecular distillation apparatus, our omega-3 yield increased by 35% with no thermal damage. The compact design slashed solvent use by 40%, cutting costs significantly. Maintenance is straightforward, and the temperature control ensures batch consistency. It’s revolutionized our production of premium-grade supplements. We’ve since expanded its use to vitamin E and CBD isolations with equal success." – Quality Director, NutraHealth Solutions
FAQ:
What industries is the BM-230 molecular distillation apparatus suitable for?
The BM-230 is widely used in pharmaceuticals, lab purification, food/beverage processing, and essential oil extraction for thermally sensitive or high-boiling-point materials.
What is the maximum vacuum pressure achievable?
With a secondary diffusion pump, the BM-230 molecular distillation apparatus achieves a vacuum of 0.001 mbar, ideal for reducing boiling points and minimizing thermal degradation.
What temperature range does the heating system support?
The electric heating jacket can reach up to 250°C, while typical evaporation temperatures range 50–80°C depending on material properties.
How to select the appropriate wiper type?
Choose between roller, sliding, or hinge wipers based on feedstock viscosity. For CBD or viscous polymers, roller wipers are recommended for uniform thin-film distribution.
What pre-operation checks are essential?
Verify cooling water pressure, ensure sufficient liquid nitrogen in the cold trap, and confirm sealing between components to maintain vacuum integrity.