Are you finding it tough to separate delicate, high-boiling compounds? Unsure if short-path or molecular distillation suits your needs? Choosing the right method can feel overwhelming.
Molecular distillation is an advanced type of short-path distillation. It uses a much higher vacuum and an even shorter distance between the evaporator and condenser. This makes it best for highly sensitive, high molecular weight, or viscous materials.
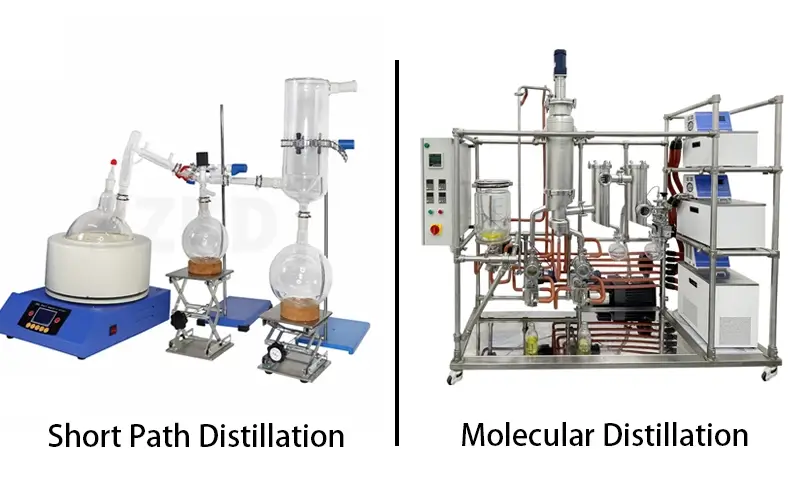
Understanding these distillation techniques is key for anyone in my field. As a manufacturer, I've seen firsthand how picking the right one can make or break a product. We want to get the purest product without damaging it. Let's explore these methods so you can make an informed choice for your laboratory or production needs.
What exactly is short-path distillation and how does it work?
Do you need to purify compounds that can't handle high temperatures? Is traditional distillation too harsh for your materials? Short-path distillation offers a much gentler way.
Short-path distillation works by reducing the operating pressure, which lowers the boiling points of substances. The vapor travels a very short distance to the condenser, minimizing product loss and heat exposure. It's great for moderately heat-sensitive materials.
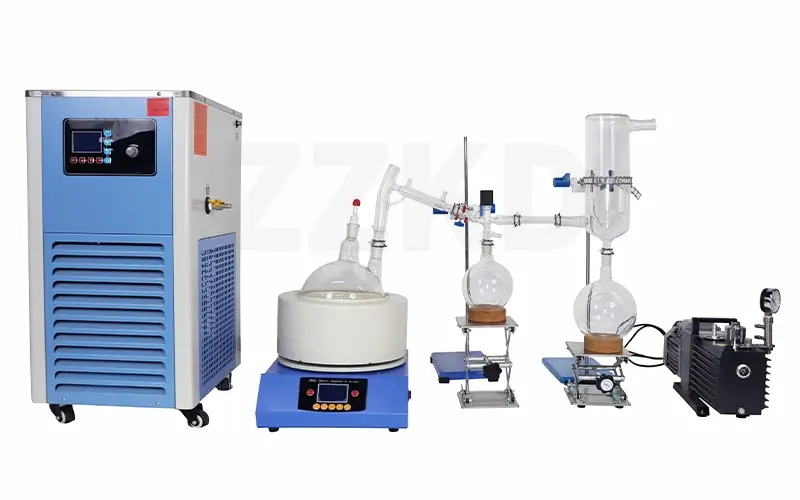
When I talk to clients about short-path distillation, I emphasize its efficiency for materials that are somewhat sensitive. Imagine you have a valuable compound that starts to break down if it gets too hot or stays hot for too long. Simple distillation might not be an option.
How Short-Path Distillation Works
In a short-path setup, the key is the short distance – often just a few centimeters – that the vaporized molecules travel from the heated surface to the condenser. Here's a simple breakdown:
Reduced Pressure: We use a vacuum pump to lower the pressure inside the system. Lower pressure means substances boil at lower temperatures. This is crucial for protecting heat-sensitive compounds.
Heating: The crude mixture is heated in a flask or vessel. The components with lower boiling points (at that reduced pressure) start to vaporize.
Short Travel: The condenser is placed very close to the evaporator. This short path means the vapor molecules condense quickly, reducing the chance of them reacting with other molecules or degrading. It also minimizes product loss on the way to the condenser.
Condensation & Collection: The purified vapors turn back into liquid on the cool condenser surface and are collected in a separate flask.
I remember a university research lab that approached us. They were working with natural plant extracts. Some of these extracts were easily damaged by heat. Using our short-path distillation equipment, they were able to isolate specific aromatic compounds much more effectively than with their old rotary evaporator setup, achieving better purity and yield. This method is a solid step up from basic distillation when you need more care for your materials.
What makes molecular distillation unique and when should I choose it?
Are you dealing with extremely heat-sensitive substances or very high-boiling point oils? Do your current distillation methods fail to give you the pure product you need? Molecular distillation could be the specialized solution.
Molecular distillation is unique because it operates under an extremely high vacuum (often below 0.001 mbar) and has an internal condenser just centimeters away from the evaporation surface. This allows separation based on molecular free path, perfect for very delicate or high molecular weight compounds.
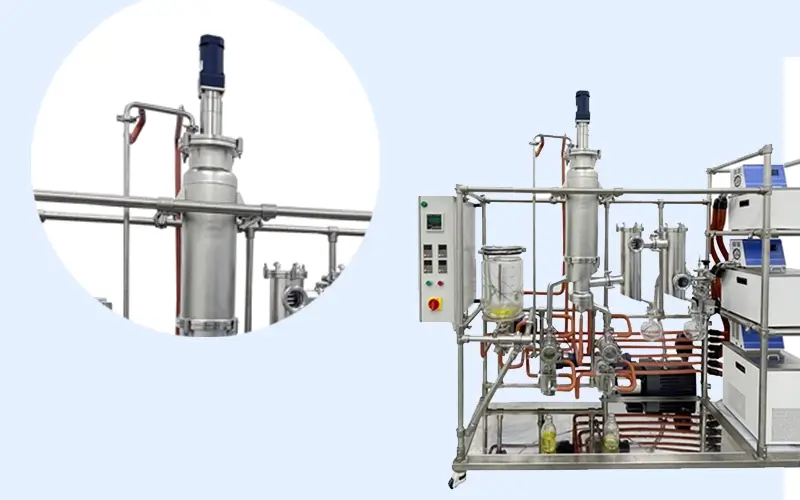
Molecular distillation, sometimes called "short path molecular distillation," takes the principles of short-path distillation to an extreme. It's the go-to method when other techniques just can't handle the job. We've designed units for clients working with everything from fish oils to complex pharmaceutical intermediates.
The Science Behind Molecular Distillation
The term "molecular free path" is central here. It’s the average distance a molecule travels before colliding with another molecule. In the ultra-high vacuum of a molecular still:
Ultra-High Vacuum: This drastically reduces the boiling point and, more importantly, increases the molecular free path of the evaporating molecules.
Internal Condenser: The condenser is located directly opposite and very close to the heated evaporating surface. The distance is typically shorter than the molecular free path of the evaporating molecules at that operating pressure.
Separation Mechanism: Molecules evaporate from the heated film. Because of the short distance and high vacuum, they are more likely to travel directly to the condenser without colliding with other gas molecules or returning to the evaporator. This separation is based more on molecular weight and less on vapor pressure differences compared to traditional distillation. Lighter molecules move to the condenser more readily.
I recall a project for a company producing high-purity Vitamin E. This compound is quite viscous and very susceptible to thermal degradation. Traditional methods were resulting in significant product loss and discoloration. When they switched to one of our molecular distillation systems, they saw a dramatic improvement in purity and color, and their yield increased significantly. That's because molecular distillation minimizes the time the material is exposed to heat – it's a very brief "flash" evaporation.
Choose Molecular Distillation System when you are processing:
Materials with very high boiling points (e.g., >250°C at atmospheric pressure).
Highly heat-sensitive substances that degrade easily.
Viscous liquids or oils that are difficult to handle in other systems.
Compounds requiring ultra-high purity.
What are the key advantages of using molecular distillation for my processes?
Do you want to get the absolute best purity for your valuable materials with the least amount of heat damage? Are you looking for an efficient way to separate tough compounds? Molecular distillation offers major benefits.
Molecular distillation gives you lower operating temperatures, which means less thermal stress and reduced degradation of your product. It results in higher purity products and can efficiently process viscous, high-boiling materials, often in a single pass.
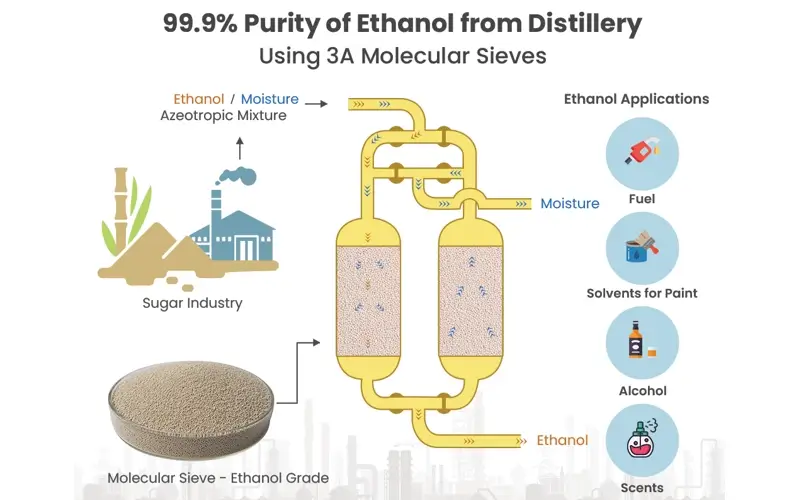
As a manufacturer who has specialized in this equipment for over 16 years, I've seen our clients achieve remarkable results by adopting molecular distillation. The advantages are not just theoretical; they translate into real-world benefits in terms of product quality and process efficiency.
Why Molecular Distillation Excels
Minimal Thermal Degradation: This is the biggest plus. The combination of ultra-high vacuum (lowering the boiling point significantly) and extremely short residence time on the heated surface (often mere seconds) means your precious molecules are exposed to heat for the shortest possible duration. This is vital for cannabinoids, omega-3 fatty acids, vitamins, and fine chemicals.
Higher Purity Products: Because separation is so efficient and thermal degradation is minimized, you often get a much purer end product. It can remove color bodies, odors, and unwanted byproducts that other methods leave behind.
Processing of High Boiling and Viscous Materials: Many materials that are practically "undistillable" by other means can be purified using molecular distillation. Think of heavy oils, waxes, resins, and polymers. The internal condenser and high vacuum handle these challenging substances effectively.
Improved Color and Odor: For products where appearance and smell are critical (like cosmetics or food ingredients), molecular distillation can significantly improve these qualities by removing volatile impurities and color precursors.
Continuous Operation Potential: Many of our molecular distillation units can be configured for continuous feeding and discharge, making them suitable for larger-scale production, which improves throughput and consistency.
One of our customers in the specialty chemicals sector was struggling to purify a synthetic ester. It was very viscous and had a high boiling point. Their attempts with wiped-film evaporation (a type of short-path) were okay, but the purity wasn't meeting their client's strict specifications. After consulting with us and investing in a molecular distillation system, they were able to achieve the target purity, reduce processing time, and ultimately secure a larger contract. It’s these successes that really show the power of this technology.
How do I select the right distillation equipment for my specific needs?
Are you feeling unsure about choosing between short-path and molecular distillation? Worried about making a costly mistake by investing in the wrong equipment? Picking the right system is absolutely crucial for your success.
To choose correctly, carefully consider your material's heat sensitivity, boiling point, and viscosity. For very delicate, high-boiling, or highly viscous substances, molecular distillation is usually superior. Short-path distillation is generally a good choice for moderately sensitive materials.
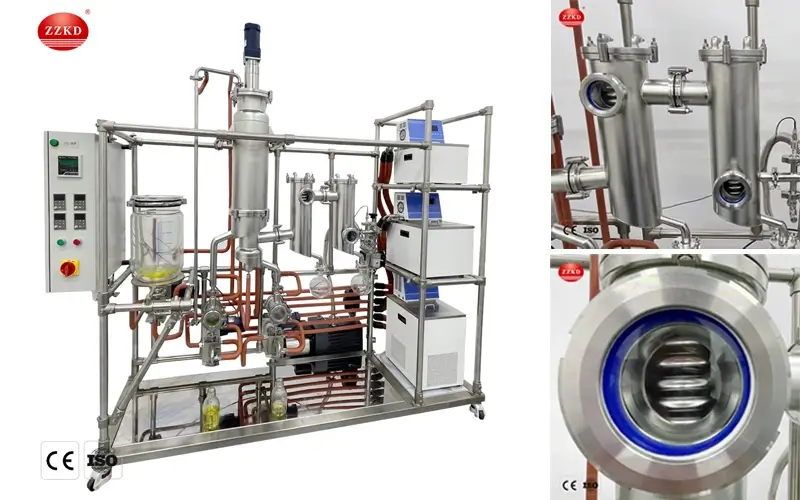
Helping customers select the right equipment is a big part of what we do. It's not just about selling a machine; it's about providing a solution. There's no one-size-fits-all answer, but by asking the right questions, we can guide you effectively.
Key Factors for Your Decision
Here's a simple comparison and some questions I typically ask my clients:
Feature / Consideration | Short-Path Distillation | Molecular Distillation |
---|---|---|
Operating Vacuum | Typically 1 to 0.001 mbar | Typically |
Heat Sensitivity of Material | Good for moderately sensitive materials | Excellent for highly sensitive, easily degradable materials |
Boiling Point of Material | Suitable for materials with moderately high boiling points | Ideal for very high boiling point materials |
Viscosity of Material | Can handle moderate viscosity | Better for highly viscous materials |
Achievable Purity | Good to very good | Very good to excellent/ultra-high |
Investment Cost | Generally lower | Generally higher |
Complexity | Simpler operation | More complex, requires precise control |
Questions to Ask Yourself:
What are the precise properties of my feed material? (Boiling range, molecular weight, viscosity, thermal stability data if available)
What level of purity do I need to achieve in the final product? Are there specific impurities I need to remove?
What is my desired throughput? (Lab scale, pilot scale, or full production scale?) This will influence the size and type of unit.
What is my budget for the equipment and its operation? While molecular distillation might have a higher upfront cost, the long-term benefits in yield and purity can justify it.
Do I have experience with high-vacuum systems? Molecular distillation requires more expertise to run optimally.
I always encourage clients to share as much information as possible about their application. Sometimes, we even suggest pilot testing if there's uncertainty. For example, a client in the cannabis industry was unsure if they needed molecular distillation for their CBD oil or if a robust short-path system would suffice for THC remediation and terpene separation. We discussed their specific end-product goals and feedstock quality, guiding them to the most cost-effective and efficient solution. Our aim is to build long-term trust by ensuring you get equipment that truly meets your needs.
Conclusion
Molecular distillation offers unparalleled precision for sensitive, high-boiling materials. Short-path distillation is great for moderate needs. Understanding your material is key to choosing wisely.